Silicon Carbide as a Material for MEMS Devices
Understanding the Basics of MEMS
The diminutive world of Microelectromechanical systems—MEMS in brief, often find themselves furnished with electronic and mechanical elements. These sophisticated systems can embody anything from simplistic structures to staggeringly intricate electromechanical assemblies with a multitude of moving parts governed by integrated circuits. The adoption of silicon carbide (SiC) as a construction material for these MEMS devices is on the rise, giving credit to its superior attributes like resilience against intense temperatures and tough environments.
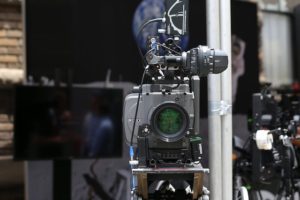
Lately, an exhaustive examination of silicon carbide has brought forth its potential suitability for high-temperature applications within MEMS technologies. SiC stands out as a prime selection due to its remarkable thermal steadiness, chemical neutrality, and firm mechanical toughness. In particularity, 3C-SiC—a polytype variation of SiC—is showing promise within harsh-environment MEMS due to its capacity to endure extreme conditions without wearing down or losing functionality. This endows it with significant relevance specifically within sensor technology encompassing industries like aerospace where equipment demands reliable operation under stringent circumstances.
Moreover, the sphere of electronic applications holds much promise in reaping benefits from advancements made in SiC-based MEMS devices. Studies conducted by IEEE on microelectromechanical systems propose that SiC could potentially usher in revolutionary changes across various facets including power electronics and radio frequency applications among others. Yet despite such promising characteristics there are still hurdles pertaining to processing methods and manufacturing costs which require resolution before commercial proliferation can be achieved at large-scale levels. Nevertheless—an optimistic future beckons this versatile material amid both established sectors as well emerging niches under the vast umbrella that is MEMS technology.
Diving Deep into the Properties of 3C-SiC
In the realm of MEMS applications, 3C-SiC has emerged as a hot ticket item. The allure? It holds its own in high-temperature environments – no small feat indeed. A closer examination of this gem reveals it’s not just one quality that sets it apart but a combination: exceptional mechanical toughness, thermal stability and resistance to chemical changes.
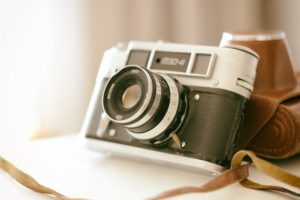
Digging deeper into silicon carbide’s composition unearths its superior hardness and strength compared to other players like polycrystalline silicon. Add to this an impressive ability to stand tall under soaring temperatures without significant wear and tear, making it an ideal candidate for substrate during fabrication.
The process of fabricating with SiC is not without intricate nuances; etch and deposition processes are part of the drill. The thin-film deposition method offers precision control over the thickness of SiC layer on substrates – a must-have for creating reliable sensors and actuators. Tweaking electronic device characteristics per certain requirements also comes into play through doping procedures at fabrication stage itself . An example being piezoresistive accelerometers crafted from doped SiC showcasing enhanced sensitivity owing to their resonance at specific frequencies.
As we shift focus towards application areas , there’s growing curiosity around deploying SiC MEMS devices in harsh conditions where traditional materials stumble or barely make the grade such as aerospace or automotive sectors . These industries require components that can endure scorching temperatures while keeping optimal performance intact – here 3c-SiC steals the limelight courtesy its inherent material traits including resilience against nitride formation even under extreme heat .
Furthermore , renowned publications by Proceedings Of The IEEE have thrown light on potential RF (Radio Frequency) technology applications due to micromechanical resonator capabilities which remain effective even when temperature scales up unlike single crystal counterparts . Thus our journey with this adaptable compound continues opening new doors as we march forward exploring fresh potentials.
Exploration of Silicon Carbide in MEMS Applications
The unveiling of Silicon Carbide (SiC) as an optimal material for MEMS applications has caused quite a stir, due to its distinctive mechanical and electronic attributes. The potential that SiC devices, particularly silicon carbide microelectromechanical systems (MEMS), have demonstrated in the realm of solid-state electronics, power contrivances, and high-temperature utilizations is nothing short of noteworthy. This semiconductor substance stands out with its unparalleled thermal conductivity and chemical stability when juxtaposed with traditional materials such as polycrystalline silicon carbide – making it a worthy contender to supplant Si in diverse electronic applications.
Researchers from the University of Edinburgh embarked on a comprehensive review which underscored the significant strides taken towards development of SiC-based apparatuses. Their focus was primarily centred upon cubic silicon carbide or 3C-SiC thin films cultivated on silicon substrates. These films boast exceptional mechanical properties rendering them perfect for MEMS sensor fabrication like pressure sensors. Inside these SiC films are tightly bonded Silicon atoms culminating into sturdy MEMS structures capable of enduring severe circumstances including extreme temperatures and pressures without any performance degradation.
Playing an integral role in fabricating these semiconductor devices is the etching process where electric fields are employed to generate coupled plasma for precision etching off silicon carbide layers from substrates. This intricate technique empowers experts to carve complex patterns essential for advanced device designs while preserving their structural integrity under operational stresses. Notwithstanding challenges linked with this method, progress persists towards fine-tuning processes implicated in manufacturing top-notch quality SiC films aptly suited for varied MEMS applications; ones demanding resilience against elevated temperatures being no exception.
High-Temperature Applications of MEMS Devices
There’s been an exhaustive exploration and progression focused on MEMS devices, with a particular emphasis on applications that can withstand high temperatures. The spotlight has fallen onto Silicon Carbide (SiC), which outperforms traditional silicon in terms of its exceptional properties.
The primary use for SiC substrates lies in the construction of devices, largely due to their extraordinary thermal stability – an appealing trait for temperature-sensitive uses. A thin layer of silicon carbide applied to these substrates elevates performance even further, exceeding what is achievable with conventional silicon technology.
High-temperature MEMS devices crafted from SiC wafers have broken new ground, paving the way for applications that can function effectively under extreme conditions where standard apparatus still struggles. To illustrate this point: 3C-SiC films grown on SiC bases endure higher temperatures compared to those made from silicon dioxide – a material frequently used as a mask during MEMS production processes. This progress has triggered the development of innovative device types and usage examples previously impossible using conventional materials such as bulk silicon or carbon.
A look at the rich array of successful executions relating to SiC-based MEMS found within reference resources proves enlightening; ranging from high-frequency functions like resonators and oscillators through to sensors tailored for severe environments. Enhancements in deposition methods offer opportunities for further refinement; improvements could lead to superior control over film thickness uniformity and surface roughness – qualities noted recently during presentations at IEEE International Conference discussing future pathways including more sophisticated designs incorporating multi-layer structures or alternative combinations of materials exploiting unique characteristics at nanoscale levels tailor-made towards specific industry requirements.
Comments are closed.