Understanding Silicon Carbide and its Properties
In the realm of semiconductors, Silicon Carbide (often symbolized as SiC) sits proudly upon a pedestal, lauded for its thermal attributes. A unique concoction of silicon and carbon elements, it stands tall against conventional materials such as silicon – besting them in multiple aspects like electrical resistance and thermal conductivity. It owes its birth to the Acheson process; a high-temperature procedure that marries pure quartz sand with petroleum coke (carbon), under temperatures escalating to 2500 degrees Celsius. This sizzling affair metamorphoses into magnificent Silicon Carbide crystals.
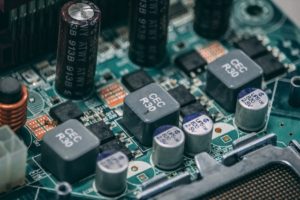
Fabricating Silicon Carbide is an art form governed by precision – unfurling across myriad stages. The journey commences with the creation of SiC powder from coarse particles through grinding machines crafted solely for this mission. Following this transformation, sintering steps onto the stage – a method of heat treatment where our protagonist is plunged into blisteringly hot temperatures yet shy from melting point – coaxing it into single-crystal structures without reducing it to liquid.
The emergence of these single-crystal wafers marks another milestone in their voyage; they are processed further into semiconductors whose applications stretch far and wide – from automotive electronics to power devices, all owing to their resilience against extreme voltages and temperatures. A spectrum exists within Silicon Carbides based on how they’re employed; certain variants are tailored meticulously depending on their synthesis or treatment during production phases. For example, some might be more suitable for high-power electronic gadgets whereas others may serve superior thermal management purposes in realms demanding such prowess – aerospace engineering components or LED lighting systems being key examples.
“Exploring the Production Process of Silicon Carbide (SIC)”
The birth of Silicon Carbide (SiC) is a thrilling dance of complexity, an intricate ballet that unfolds in stages. It all commences with the initial synthesis of silicon and carbon. A unique blend of silica sand and carbon is carefully composed – hand in hand they step into the heated spotlight known as the resistance furnace, or more romantically referred to as an Acheson furnace.
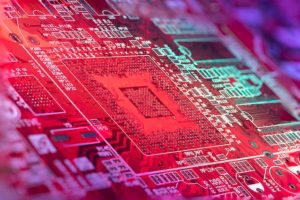
This high-temperature stage gently stirs a reaction between these two raw materials, culminating in the formation of SiC grains through what is poetically named after its creator – The Acheson process.
But this waltz does not end here; it’s just intermission. These newly synthesized SiC particles now embark on a journey towards refinement, enhancing their glorious attributes like hardness and thermal conductivity. Sintering emerges from backstage – a heat treatment applied under pressure that enables particle size control while upholding the material’s inherent toughness and abrasive nature.
Introduced next onto our production stage is crystal growth on a silicon carbide substrate; it’s akin to crafting delicate lace where single crystals are skillfully formed from vapor deposition onto the substrate surface—an act so intricate yet essential.
And let us not forget grinding—a performer who perhaps doesn’t get enough applause but plays an integral role nonetheless—shaping rough edges into smooth surfaces for better usability in applications such as semiconductors or other electronic devices requiring precision without sacrificing performance attributes like chemical resistance or thermal conductivity capabilities.
Each performance—from synthesizing raw materials like silica sand and carbon with machines called resistance furnaces to forming single crystals via vapor deposition techniques—are coordinated steps contributing towards creating top-tier Silicon Carbide products catering to diverse industrial needs. Thus concludes our breathtaking ballet—the tale behind producing high-quality SiC products.
“Silicon Carbide: From Wafer to Semiconductor”
A mystical fusion of carbon and silicon results in the creation of Silicon Carbide, a process teeming with complexity. This intricate dance involves the union of silica (SiO2) and carbon (C), heated intensely within electric resistance furnaces, mirroring the chemical formula for its birth. The mastermind behind this elaborate procedure was Edward Goodrich Acheson, who pioneered it during the twilight of the 19th century using his namesake graphite electrodes. As time unraveled, refinements were added to enhance quality.
The performance begins with minuscule grains of silicon carbide powder uniting with high-purity silicon and carbon powders in an intimate blend. These ingredients then brave blazing temperatures within an electric furnace until they meld into one entity. Upon cooling, SiC wafers emerge which are further subjected to heat under disciplined circumstances resulting in a layer rich in Silicon Carbide on top. Like boron carbide or even diamond’s extreme hardness; thermal stability that defies comparison; outstanding electrical conductivity – all these properties make them perfect candidates as semiconductors.
Beyond their role as semiconductors, Silicon Carbides drape themselves across various scenarios due to their unique characteristics—Silicon Nitride bonded Silicon Carbide finds itself extensively warming up as heating elements capable of enduring scorching hot temperatures without faltering. Moreover, when Gallium Nitride is introduced via Chemical Vapor Deposition(CVD), power devices spring into existence functioning at sky-high voltage levels more efficiently than traditional semiconductors while minimizing energy losses notably during operation . Yet another instance sees SiC powders metamorphose into highly resistant silicon carbide fibers revered by multiple industries including aerospace where they bolster composite materials owing to their superior strength-to-weight ratio.
“Types of Machines Used in Silicon Carbide Production”
In the labyrinthine journey of silicon carbide production, a multitude of machines are enlisted. A standout device in this convoluted machinery is the Acheson graphite electric resistance furnace – an old-timer contraption born from Edward Goodrich Acheson’s ingenuity back in 1892, and still fiercely relevant today.
The furnace embarks on its duty by cranking up temperatures between 1600°C to 2500°C as it hosts a union of silica or quartz sand and high-purity carbon powder under nitrogen gas supervision. The heat rouses the surplus carbon from organic matter into a dance with oxygen, birthing CO2 and leaving behind Silicon Carbide (SiC) – a compound that plays hard-to-get with nature but submits readily to this method. This SiC offspring boasts minimal thermal expansion – having little fondness for stretching when heated; its rigidity and thermal conductive prowess make it sought-after in various spheres including mirror material for astronomical telescopes.
Another cog in this intricate process is equipment tailored explicitly for gauging surface roughness – an essential barometer signalling quality control during manufacturing choreography. These tools also double as temperature detectives within pyrometry – an optical technique used to monitor gas temperatures; these readings form crucial data points needed to maintain ideal sintering conditions where particles coalesce to spawn dense components without succumbing completely to liquid transformation.
Interestingly enough, despite possessing remarkable thermal shock resistance abilities largely due to its unique structure composed of tightly-bound covalent bonds created after unsuccessful attempts at dissolving carbon within molten corundum solution earlier on throughout fabrication stages.
Comments are closed.